Community
Fired by collaboration: Artists and industry partner to improve public spaces
Jan Swoope
July 1, 2011 11:14:00 PM
Article from www.cdispatch.com
The couple work deep within the recesses of Columbus Brick Co., off Military Road. There, acres of metal buildings envelop a network of railcar lines and imposing machinery. For more than a century, craftsmen have produced literally millions of bricks at the local yard.
In an extension of that process, the Colemans are turning raw Mississippi shale and clay into a mini-park centerpiece, thanks to a partnership between arts and industry.
The sculpture in progress was commissioned for the new Haire Wealth Management Green Space in downtown Tupelo, but the collaboration that birthed it is a model for any community.
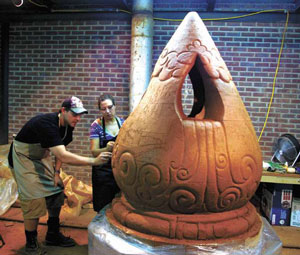
“It’s as labor intensive — but as simple — as you can imagine,” said Tanner Coleman. The sculptor stood back, assessing progress on a three-ton brick artwork he and his wife, Alexis, have invested heart and hands in for the past few weeks. Smudged faces and clay-crusted fingers attested to the long, hot hours put in that day.
The couple work deep within the recesses of Columbus Brick Co., off Military Road. There, acres of metal buildings envelop a network of railcar lines and imposing machinery. For more than a century, craftsmen have produced literally millions of bricks at the local yard.
In an extension of that process, the Colemans are turning raw Mississippi shale and clay into a mini-park centerpiece, thanks to a partnership between arts and industry.
The sculpture in progress was commissioned for the new Haire Wealth Management Green Space in downtown Tupelo, but the collaboration that birthed it is a model for any community.
Good neighbors
Family-owned Columbus Brick Co. has been quietly supporting the ceramic art world for a number of years.
When asked about that interest, company president Al Puckett offered, “You know, I think people (often) think our process out here looks very mechanical, very much like it’s all science, technology and a set recipe. But there’s a lot of art inherent in what we do.”
He continued, “The fact is that we go out and find something in the ground that’s not a vendor-supplied, quality controlled material; we take that and make that into a brick. This stuff doesn’t always behave the same when we form it or apply temperature to it. … It’s an art form. And these folks (clay artisans) understand that; they’re working with the same medium. … As a good corporate citizen, it’s something we enjoy supporting.”
The sculptors are grateful for materials, workspace and kiln all under one roof, a luxury often unavailable when they work in smaller, private studios.
“This brick came from here; it wants to be fired in these kilns,” said Tanner.
Hands on
In the designated “studio” space at the brickyard, flat railcars resembling solid, super-sized pallets on wheels are stacked high with “green,” or “wet,” blocks of clay. About 800 of them went into the sculpture measuring 7 1/2 feet tall and about 4 feet in width.
“When we first started putting it together, it was basically a Lego construction,” said Tanner, a recipient of an individual artist’s grant fellowship from the Mississippi Arts Commission.
With specialized tools and great patience, husband and wife painstakingly transformed the mountain of raw clay into the overall shape of a water drop or raindrop. Designs of flowing water and clouds were added. Their concept represents the history of the new green space site, one of Tupelo’s first water and TVA power storage locations.
Both artists are talented in other mediums, but clay brick is their collaborative niche, one rich with possibilities for functional public art, such as bench seating, planters, archways, water features and wall murals.
“Brick allows us to build any shape, any form; the limitations are very few,” explained Tanner, watching as Alexis slowly circled the sculpture with a sprayer, evenly wetting the surface to keep the clay from drying out. “It kind of reveals itself as you work with it, and takes the piece where it needs to go. … But there’s no part of the process that’s fast.”
End stages
Ironically, the sculpture will soon be disassembled before firing, a process that will take four or five days. Reassembly and installation in Tupelo is expected to take about a week. Then, the new green space will be well on its way.
Sharing a philosophy applicable everywhere, Lewis of JBHM stated, “Designing places that are attractive and that are good places for people to interact in a community is what helps it thrive. You create spaces where people will be happy to be, and they stay to window shop, eat in the restaurants, go to the book store … you create that thriving downtown environment that doesn’t shut down at 5 when people get off work.”
The green space is only one small piece of the puzzle.
“You have to engage these processes one step at a time,” he said, “whenever you have an opportunity to make an improvement in one piece of the community — and you start knitting those pieces together.”
For the Colemans, it’s all about doing something bigger than themselves.
“To me, being a sculptor means being a public artist, an architectural ceramist, object and mold-maker, potter, foundry-man, welder, and carver,” expressed Tanner. “I’m very excited about the idea of working in the walls of any industry and to be a part of history.”
For Alexis, “The improvement of human spaces fuels my desire to create. … The greater reason we do this, as corny as it sounds, is that it’s a way of making a difference in communities and impacting people’s lives.”
CBC Employees Visit Middle School
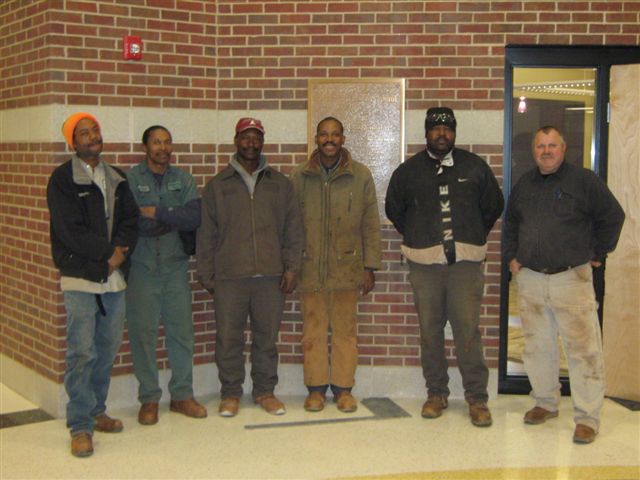
Global Connections
A portion of the profit of Columbus Brick goes to support Global Connections and their partners in Kenya – www.globalconnectionsonline.org. Many of the employees of Columbus Brick also contribute a portion of their salaries to help the children at the Limuru Children’s Centre and Orphanage as well as other partners which Global Connections serves in Kenya.
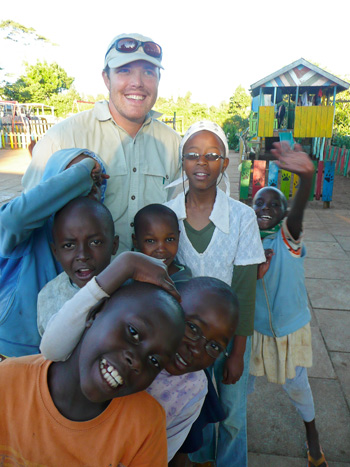
Helping Katrina Relief
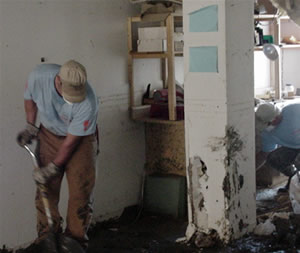
Doug Brown working with the Katrina clean-up.
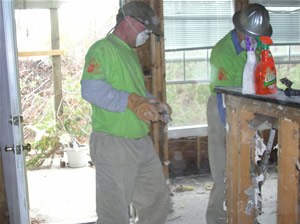
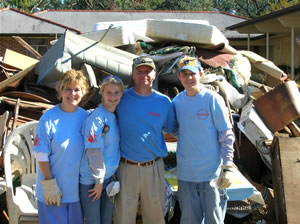
Butch, Margaret, Tyler & Betsy helping with Katrina clean-up.
Columbus Brick Employees donate time to help build local boys and girls club
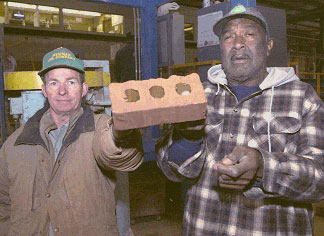
By Ann M. Tabb
The Commercial Dispatch
March 22, 2002
Columbus Brick Company employees on Friday put their skills to work by helping create the foundation for the new local boys & Girls Club.
Plant 1 Manager Mike Dowd said that 58,000 bricks were made between 6 and 9:30 a.m. at the plant, located at 114 Brickyard Road.
The bricks were made by using raw clay donated by the family of company president and chairman Al Puckett.
All 20 volunteers signed up and came in on their own accord and on their own time and on a chilly morning, no less,” Dowd said.
Bobby Marshall and Eugene Chapman show off one of the many bricks to be used in the construction of the Boys & Girls Club. Photo by Kelly Tippett, Dispatch Staff.
Dowd and three volunteers from Columbus were warming up with coffee next to the plan’s huge dryer, where the bricks will rest for the next four days before a final hardening in a 2,100-degree kiln.
Machine Operator Leroy Stinson said that he attended the Boys & Girls Club as a child.
Stinson, a soft-spoken machine operator, said that he just wanted to come out with his fellow machine operators to “help the club get off its feet.”
Machine Operator Willie Wilson was a YMCA kid growing up, but he took the opportunity to help out what he believes is a worthy cause.
“I came out to give a little time because the children need a place to play and to stay in off the street,” Wilson said. “It is dangerous out there.”
Clarence Sherrod, who moved from Chicago to Columbus 11 months ago, said he has a lot of nephews and cousins who cannot wait for the center to open.
“It will be enjoyable to watch the kids have some fun in the new place once it opens,” said Sherrod, who lives across the street from the site of the new club.
Sherrod operated a “pug,” a machine that starts and stops the brick making process by determining the hardness of the bricks.
In December, ground was broken on the site of the $1 million future home of the club, to be located along 14th Avenue North. Tentative plans are to move the club from its 20th Street location in July 2002.
MSU School of Architecture Students Get Some On Hand Experience
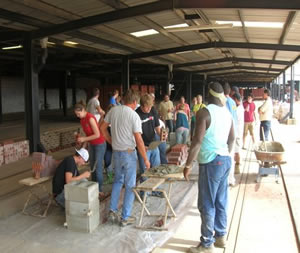
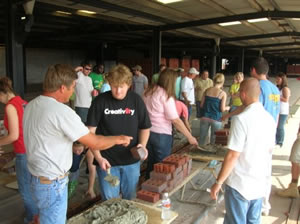
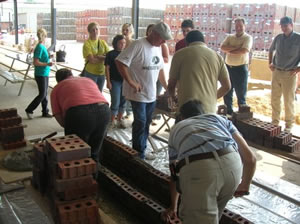
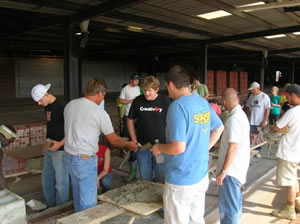
Community
Fired by collaboration: Artists and industry partner to improve public spaces
Jan Swoope
July 1, 2011 11:14:00 PM
Article from www.cdispatch.com
The couple work deep within the recesses of Columbus Brick Co., off Military Road. There, acres of metal buildings envelop a network of railcar lines and imposing machinery. For more than a century, craftsmen have produced literally millions of bricks at the local yard.
In an extension of that process, the Colemans are turning raw Mississippi shale and clay into a mini-park centerpiece, thanks to a partnership between arts and industry.
The sculpture in progress was commissioned for the new Haire Wealth Management Green Space in downtown Tupelo, but the collaboration that birthed it is a model for any community.
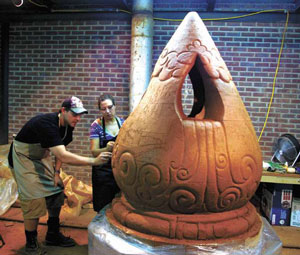
“It’s as labor intensive — but as simple — as you can imagine,” said Tanner Coleman. The sculptor stood back, assessing progress on a three-ton brick artwork he and his wife, Alexis, have invested heart and hands in for the past few weeks. Smudged faces and clay-crusted fingers attested to the long, hot hours put in that day.
The couple work deep within the recesses of Columbus Brick Co., off Military Road. There, acres of metal buildings envelop a network of railcar lines and imposing machinery. For more than a century, craftsmen have produced literally millions of bricks at the local yard.
In an extension of that process, the Colemans are turning raw Mississippi shale and clay into a mini-park centerpiece, thanks to a partnership between arts and industry.
The sculpture in progress was commissioned for the new Haire Wealth Management Green Space in downtown Tupelo, but the collaboration that birthed it is a model for any community.
Good neighbors
Family-owned Columbus Brick Co. has been quietly supporting the ceramic art world for a number of years.
When asked about that interest, company president Al Puckett offered, “You know, I think people (often) think our process out here looks very mechanical, very much like it’s all science, technology and a set recipe. But there’s a lot of art inherent in what we do.”
He continued, “The fact is that we go out and find something in the ground that’s not a vendor-supplied, quality controlled material; we take that and make that into a brick. This stuff doesn’t always behave the same when we form it or apply temperature to it. … It’s an art form. And these folks (clay artisans) understand that; they’re working with the same medium. … As a good corporate citizen, it’s something we enjoy supporting.”
The sculptors are grateful for materials, workspace and kiln all under one roof, a luxury often unavailable when they work in smaller, private studios.
“This brick came from here; it wants to be fired in these kilns,” said Tanner.
Hands on
In the designated “studio” space at the brickyard, flat railcars resembling solid, super-sized pallets on wheels are stacked high with “green,” or “wet,” blocks of clay. About 800 of them went into the sculpture measuring 7 1/2 feet tall and about 4 feet in width.
“When we first started putting it together, it was basically a Lego construction,” said Tanner, a recipient of an individual artist’s grant fellowship from the Mississippi Arts Commission.
With specialized tools and great patience, husband and wife painstakingly transformed the mountain of raw clay into the overall shape of a water drop or raindrop. Designs of flowing water and clouds were added. Their concept represents the history of the new green space site, one of Tupelo’s first water and TVA power storage locations.
Both artists are talented in other mediums, but clay brick is their collaborative niche, one rich with possibilities for functional public art, such as bench seating, planters, archways, water features and wall murals.
“Brick allows us to build any shape, any form; the limitations are very few,” explained Tanner, watching as Alexis slowly circled the sculpture with a sprayer, evenly wetting the surface to keep the clay from drying out. “It kind of reveals itself as you work with it, and takes the piece where it needs to go. … But there’s no part of the process that’s fast.”
End stages
Ironically, the sculpture will soon be disassembled before firing, a process that will take four or five days. Reassembly and installation in Tupelo is expected to take about a week. Then, the new green space will be well on its way.
Sharing a philosophy applicable everywhere, Lewis of JBHM stated, “Designing places that are attractive and that are good places for people to interact in a community is what helps it thrive. You create spaces where people will be happy to be, and they stay to window shop, eat in the restaurants, go to the book store … you create that thriving downtown environment that doesn’t shut down at 5 when people get off work.”
The green space is only one small piece of the puzzle.
“You have to engage these processes one step at a time,” he said, “whenever you have an opportunity to make an improvement in one piece of the community — and you start knitting those pieces together.”
For the Colemans, it’s all about doing something bigger than themselves.
“To me, being a sculptor means being a public artist, an architectural ceramist, object and mold-maker, potter, foundry-man, welder, and carver,” expressed Tanner. “I’m very excited about the idea of working in the walls of any industry and to be a part of history.”
For Alexis, “The improvement of human spaces fuels my desire to create. … The greater reason we do this, as corny as it sounds, is that it’s a way of making a difference in communities and impacting people’s lives.”
CBC Employees Visit Middle School
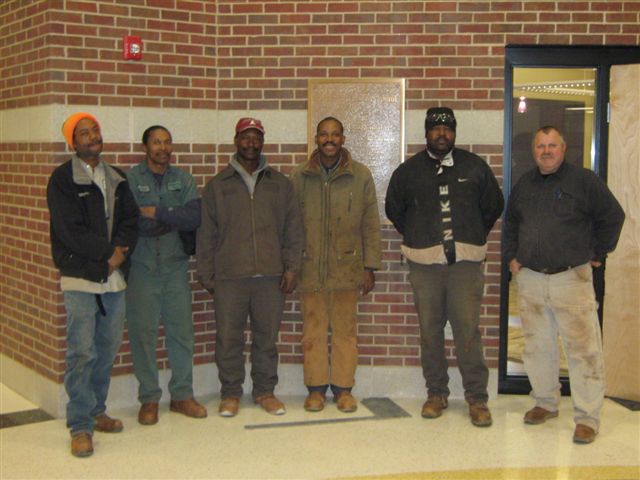
Global Connections
A portion of the profit of Columbus Brick goes to support Global Connections and their partners in Kenya – www.globalconnectionsonline.org. Many of the employees of Columbus Brick also contribute a portion of their salaries to help the children at the Limuru Children’s Centre and Orphanage as well as other partners which Global Connections serves in Kenya.
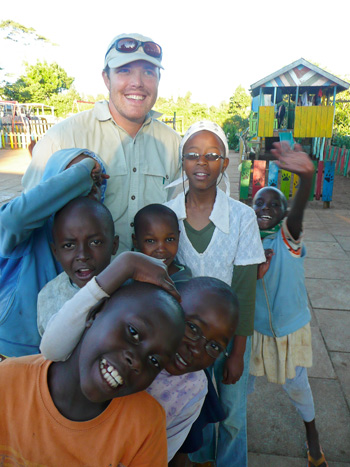
Helping Katrina Relief
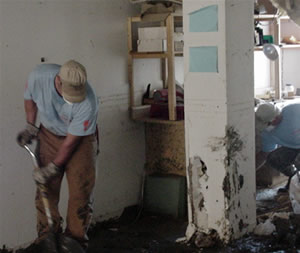
Doug Brown working with the Katrina clean-up.
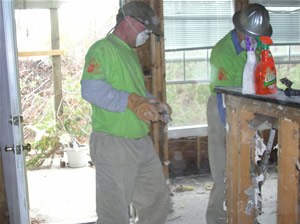
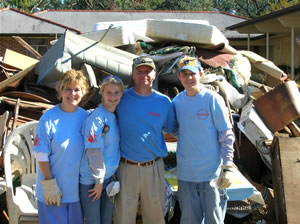
Butch, Margaret, Tyler & Betsy helping with Katrina clean-up.
Columbus Brick Employees donate time to help build local boys and girls club
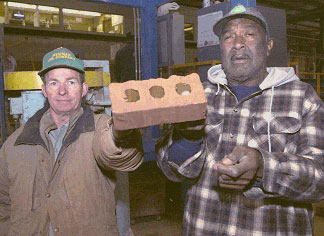
By Ann M. Tabb
The Commercial Dispatch
March 22, 2002
Columbus Brick Company employees on Friday put their skills to work by helping create the foundation for the new local boys & Girls Club.
Plant 1 Manager Mike Dowd said that 58,000 bricks were made between 6 and 9:30 a.m. at the plant, located at 114 Brickyard Road.
The bricks were made by using raw clay donated by the family of company president and chairman Al Puckett.
All 20 volunteers signed up and came in on their own accord and on their own time and on a chilly morning, no less,” Dowd said.
Bobby Marshall and Eugene Chapman show off one of the many bricks to be used in the construction of the Boys & Girls Club. Photo by Kelly Tippett, Dispatch Staff.
Dowd and three volunteers from Columbus were warming up with coffee next to the plan’s huge dryer, where the bricks will rest for the next four days before a final hardening in a 2,100-degree kiln.
Machine Operator Leroy Stinson said that he attended the Boys & Girls Club as a child.
Stinson, a soft-spoken machine operator, said that he just wanted to come out with his fellow machine operators to “help the club get off its feet.”
Machine Operator Willie Wilson was a YMCA kid growing up, but he took the opportunity to help out what he believes is a worthy cause.
“I came out to give a little time because the children need a place to play and to stay in off the street,” Wilson said. “It is dangerous out there.”
Clarence Sherrod, who moved from Chicago to Columbus 11 months ago, said he has a lot of nephews and cousins who cannot wait for the center to open.
“It will be enjoyable to watch the kids have some fun in the new place once it opens,” said Sherrod, who lives across the street from the site of the new club.
Sherrod operated a “pug,” a machine that starts and stops the brick making process by determining the hardness of the bricks.
In December, ground was broken on the site of the $1 million future home of the club, to be located along 14th Avenue North. Tentative plans are to move the club from its 20th Street location in July 2002.
MSU School of Architecture Students Get Some On Hand Experience
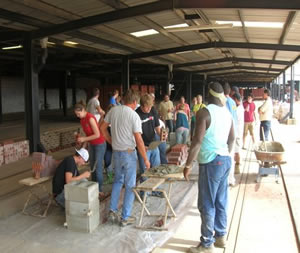
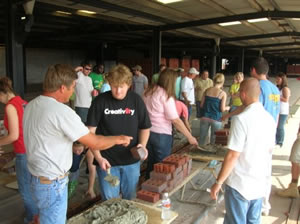
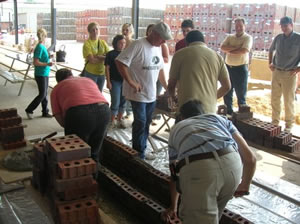
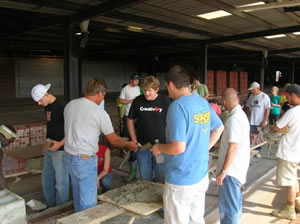